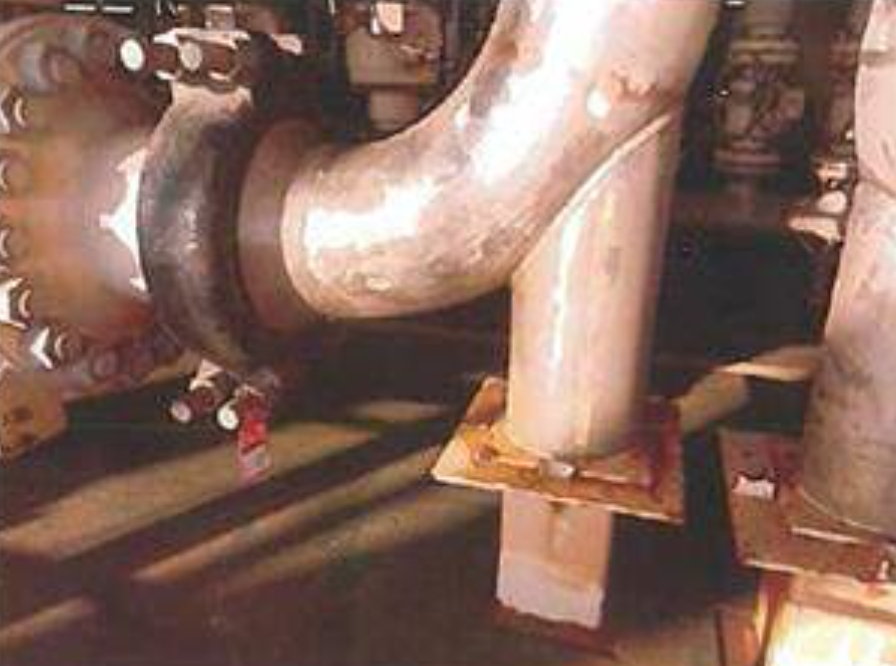
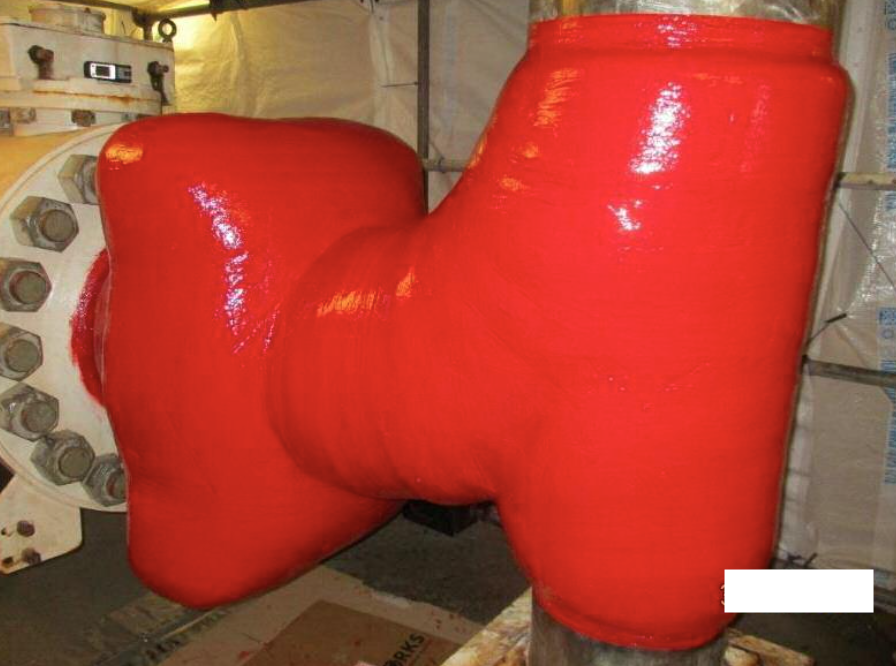
Nature of defect
The 18” water injection riser clamp joint had suffered from movement inside the retaining clamp when operating at high pressure. This had resulted in injection water leaking from inside the clamp when operating at 420 bar. The client required a composite repair to arrest and seal the leak, and to reinforce the joint with a composite overwrap capable of withstanding the high design pressures.
Solution
Metalyte Pipeworks was asked to design and engineer a composite repair which was capable of sealing the leak at the clamp joint, but also capable of withstanding the high operating and design pressures that the line will see. Metalyte Pipeworks Engineers were able to run FEA analysis on the repair solution in order prove that the repair could easily withstand the high pressures of the system.
Repair Method
The full repair area including the clamp joint was prepared to gain the required surface profile for the composite to bond to. Once the surface preparation was complete, the clamp joint was sealed, filled and built out to gain a smooth geometry for the composite to be applied to. Metalyte Pipeworks used their high compression filling compound to build up before applying a Kevlar reinforced high bond strength primer resin.
Once the primer resin was fully cured, the technicians applied the engineered composite overwrap. Metalyte Pipeworks had two teams working back to back on this scope to ensure the repair was completed in the most time-efficient way possible. A plan was implemented to ensure the work was continued with no down time in labour, whilst also ensuring full cure of each stage was achieved.The completed repair was coated our UV/chemical protective resin.